What is Asset Management?
Asset management is the process of maintaining buildings, equipment, and infrastructure to keep them working well and lasting longer. It includes checking for needed repairs, scheduling maintenance, and planning future upgrades or replacements. The goal is to make smart decisions that save money and keep everything running smoothly. Standards like ISO 55000 help guide best practices in asset management.
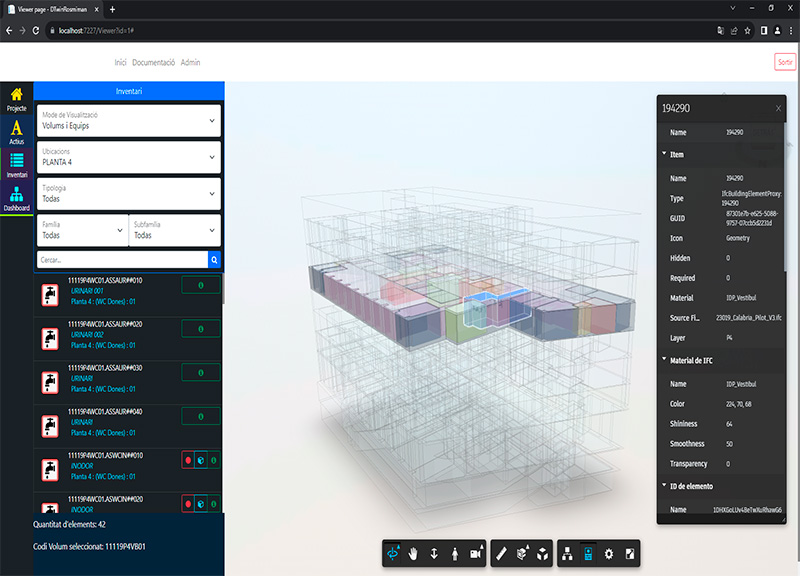
Role of BIM in Asset Management
BIM (Building Information Modeling) helps with asset management by creating detailed digital models of buildings and infrastructure. These models include information about design, materials, equipment, maintenance, and operational data. With BIM, asset managers can access up-to-date information, plan maintenance, track performance, and make better decisions. This helps save time, reduce costs, and improve how assets are managed throughout their lifecycle.
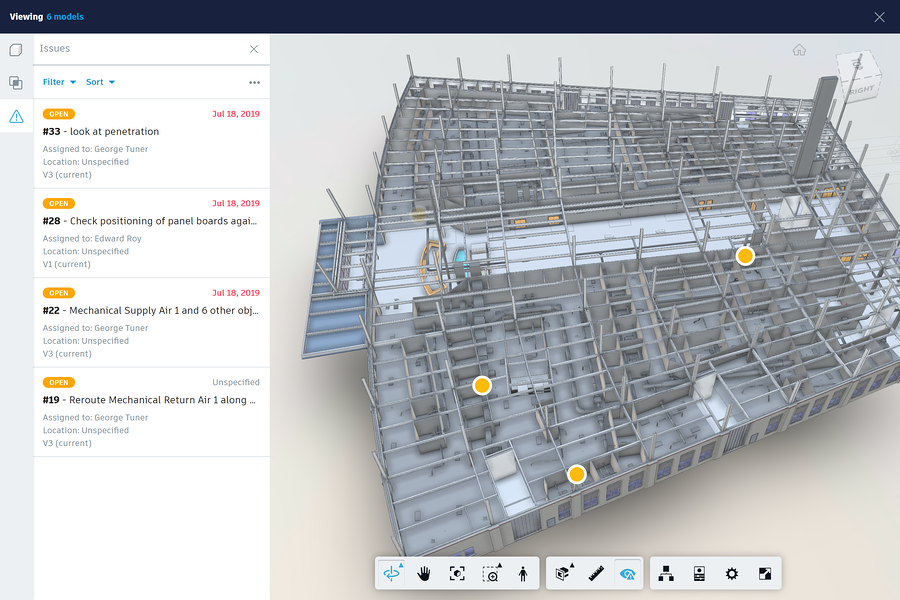
Benefits of BIM in asset management :
- Centralized Data Access: BIM creates a digital model that stores all relevant information about an asset, making it easy for asset managers to access details for maintenance, operation, and future planning.
Enhanced Maintenance Planning: BIM models include information on the location and specifications of components, helping managers plan and execute repairs and servicing more efficiently.- Better Decision-Making: By providing comprehensive, real-time data, BIM supports informed decision-making related to asset performance and life cycle management.
- Cost Savings: Streamlined maintenance and improved resource allocation through BIM lead to reduced operational costs and fewer unexpected repairs.
- Improved Collaboration: BIM allows different teams, from architects to facility managers, to work from a unified model, fostering better communication and collaboration throughout the asset's lifecycle.
- Lifecycle Management: BIM supports long-term asset management by tracking changes, updates, and historical data, which aids in planning upgrades or replacements.
- Sustainability and Efficiency: By simulating performance and energy usage, BIM can help identify opportunities for reducing resource consumption and making assets more sustainable.
Challenges of Asset Management without BIM :
Asset management without BIM faces significant challenges, including fragmented information and lack of central data storage, leading to inefficiencies and errors. Maintenance schedules, design data, and operational insights are often dispersed, making tracking and decision-making cumbersome. Visualizing asset conditions and their interdependencies becomes difficult, increasing the risk of mismanagement. Cost estimation and lifecycle planning are less accurate, resulting in higher operational expenses. Coordination between stakeholders is hindered due to limited collaboration tools. Additionally, identifying issues like wear-and-tear or equipment failures is slower, causing delays and increased downtime. Without BIM’s data-driven approach, asset management becomes reactive rather than proactive.
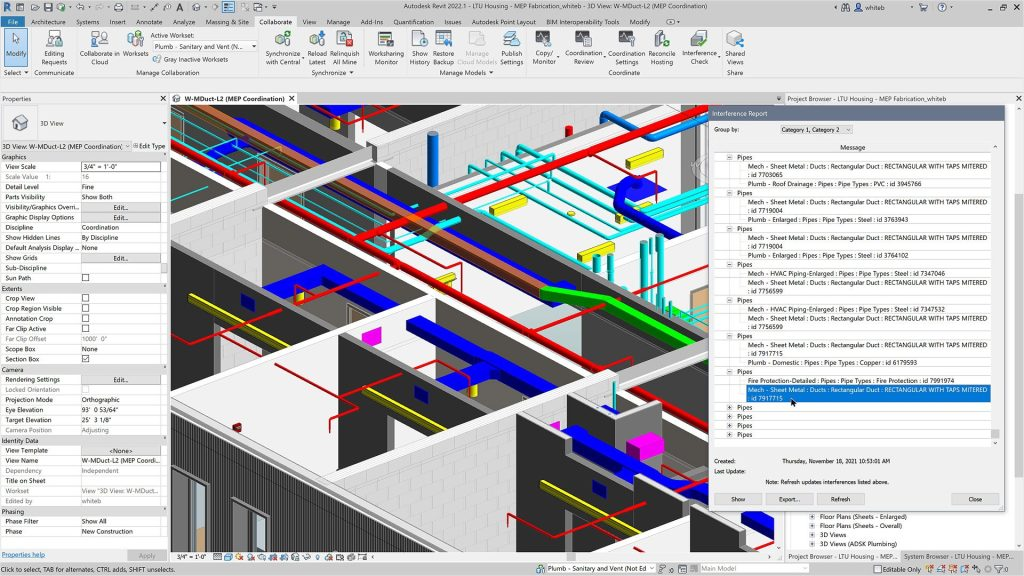
Tools for Asset Management:
- Asset Management Platforms: Tools like IBM Maximo, Infor EAM, and Oracle Primavera offer features for work order management and preventive maintenance scheduling, often integrating with BIM data.
- BIM Authoring Tools: Software such as Autodesk Revit, Bentley MicroStation, and Graphisoft ArchiCAD are used for creating BIM models and include asset management functionalities.
- BIM Viewers and Collaboration Tools: Applications like Autodesk BIM 360, Bentley Navigator, and Solibri Model Viewer enable stakeholders to visualize BIM models and collaborate on asset management tasks.
- Data Management and Integration Solutions: Tools such as Autodesk Forge, Bentley iTwin, and Nemetschek Open BIM facilitate the integration of BIM data with other asset management systems.
- Analytics and Reporting Tools: Solutions like Power BI, Tableau, and Qlik provide data visualization and reporting capabilities for analyzing asset performance and maintenance trends.
Conclusion
- Integrating Building Information Modeling (BIM) into asset management significantly benefits buildings and infrastructure organizations. BIM creates detailed digital models that help asset managers make smarter maintenance decisions, saving money and prolonging asset lifespans.
- With BIM, managers can easily track and document assets, monitor their condition, and plan maintenance effectively. This connection between BIM data and asset management improves collaboration among teams, ensuring smooth operations from design through to maintenance.
- As technology evolves, we can look forward to exciting advancements in BIM, such as the use of digital twins and new tools like augmented reality (AR) and virtual reality (VR). These innovations will make asset management even easier and more efficient, leading to better overall performance for organizations.
FAQs
What types of assets can be managed with BIM?
BIM can manage various assets, including buildings, infrastructure, equipment, and utilities. It handles physical assets like HVAC systems and digital assets like maintenance schedules, ensuring efficient operations and asset longevity.
How does BIM reduce costs in asset management?
BIM reduces costs by streamlining maintenance through accurate data, minimizing errors, and optimizing resources. It enhances predictive maintenance, reducing downtime and repair costs, and supports sustainable management practices.
What is the role of BIM in lifecycle management?
BIM facilitates comprehensive lifecycle management by integrating design, construction, operation, and decommissioning phases. It provides a central data repository for informed decision-making, ensuring efficiency and reducing lifecycle costs.
What are the future trends in BIM for asset management?
Future trends include AI-driven analytics for predictive maintenance, integration with IoT for real-time monitoring, cloud-based BIM for collaboration, and advancements in digital twins to enhance asset performance and sustainability.